About Us
Specialized in providing total solutions for heat dissipation materials
Changzhou Tiger Electronic Technology Co., Ltd. is mainly engaged in the technical development and technical consultation of heat dissipation components in the fields of power semiconductor IGBT packaging and integrated circuits, and provides overall solutions, technical services, production and sales of heat dissipation materials. According to the needs of users, we have developed a variety of SiCp/Al, diamond, aluminum diamond, copper diamond, molybdenum, molybdenum copper, tungsten copper, copper molybdenum copper, copper-molybdenum copper-copper, Kovar, and other products to provide professional thermal management materials and technical solutions for manufacturers of microwave devices, high-power devices and microelectronic devices.
Production base
Senior Technical Staff
Total assets of the enterprise
Enterprise cooperation customer
Product Series
Insist on exploratory research
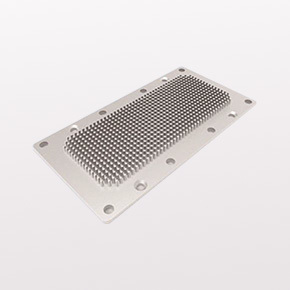
IGBT Pin Heat Dissipation Substrate

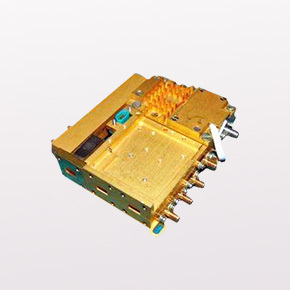

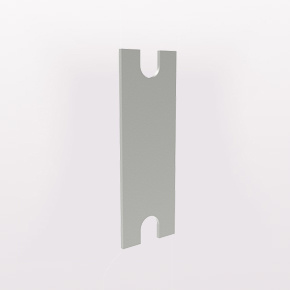

Application areas
Widely used in all major fields






News
Keep up to date with the latest news
The electronic components of the car should be reliable and durable, and need no maintenance during the life of the car. However, for electric vehicles and hybrid vehicles, electronic components must be subjected to high pressure and high temperature environment, it is necessary to have liquid cooling. Obviously, cooling technology requires careful technical research and development, and materials need to pass the assessment of reliable durability and applicability to ensure stable operation. Even with high technical requirements, OEM customers continue to pursue high-volume, low-cost, high-quality products.
For new energy vehicles, the battery, VCU, BSM, and motor efficiency all lack room for improvement. The most room for improvement is the motor drive part, and the core component of the motor drive part is IGBT(Insulated Gate Bipolar Transistor, Insulated Gate Bipolar Transistor chip) is the most important. IGBT accounts for about half of the cost of the motor drive system, while the motor drive system accounts for 15-20% of the cost of the whole vehicle, that is to say, IGBT accounts for 7-10% of the cost of the whole vehicle, which is the second highest cost component except the battery, and also determines the energy efficiency of the whole vehicle. Not only the motor drive to use IGBT, new energy generators and air conditioning parts generally also need IGBT. Not only new energy vehicles, but also the core of DC charging piles and locomotives (high-speed rail) are IGBT tubes. 30% of the raw material cost of DC charging piles is IGBT. Electric locomotives generally need 500 IGBT modules, EMUs need more than 100 IGBT modules, and a subway needs 50-80 IGBT modules. Mitsubishi Electric's HVIGBT has become the default standard in the industry. China's high-speed locomotive IGBT is completely monopolized by Mitsubishi. At the same time, Alstom, Siemens and Bombardier in Europe also use more than half of Mitsubishi Electric's IGBT. In addition to Japanese manufacturers, Infineon has taken over the IGBT of almost all electric vehicles, while mitsubishi electric is intoxicated by the huge profits of China's high-speed rail and has achieved almost nothing in the market below 2500V. In 2016, the global sales volume of electric vehicles was about 2 million, which consumed about 0.9 billion US dollars of IGBT tubes, with an average of about 450 US dollars per vehicle. It is the most expensive component in electric vehicles except batteries. Among them, there are about 770000 hybrid and PHEV vehicles, each requiring about $300 IGBT, about 1.23 million pure electric vehicles, with an average of $540 IGBT per vehicle, and IGBTs for high-power pure electric buses may exceed $1000. What is IGBT? IGBT is a composite full-control voltage-driven power semiconductor device composed of BJT (bipolar transistor) and MOS (insulated gate field effect transistor). Compared with the previous various power electronic devices, IGBT has the following characteristics: high input impedance, can use general low-cost drive circuit; high-speed switching characteristics; on-state low loss. IGBT combines the advantages of MOSFET's high input impedance and GTR's low conduction voltage drop, and has obvious advantages in comprehensive performance. It is very suitable for application in DC voltage of 600V and above converter systems such as AC motors, frequency converters, switching power supplies, lighting circuits, traction drives and other fields.
The electronic components of the car should be reliable and durable, and need no maintenance during the life of the car. However, for electric vehicles and hybrid vehicles, electronic components must be subjected to high pressure and high temperature environment, it is necessary to have liquid cooling. Obviously, cooling technology requires careful technical research and development, and materials need to pass the assessment of reliable durability and applicability to ensure stable operation. Even with high technical requirements, OEM customers continue to pursue high-volume, low-cost, high-quality products. Dana's brand LONG®Our thermal management products have many years of experience in thermal conduction solutions, providing the basis for the innovative development of insulated gate bipolar transistor (IGBT) heat sinks. Although copper has been traditionally used in automobile manufacturing for decades, it has been gradually replaced by lighter and lower-cost aluminum in recent years. The IGBT product package also goes beyond electronic solutions in the conventional sense. Today, the industry tends to use newly developed semiconductor materials to customize designs, but tailor-made product packages require thermal management equipment to meet key customer needs, such as lower cost, higher quality, and lighter weight. Dana's aluminum IGBT thermal design is an excellent solution that can effectively cool down, reduce fuel consumption, have corrosion resistance, and can even be recycled. This optimized design provides the thermal performance and rapid heat transfer required for electric and hybrid vehicles. In addition, Dana has also assembled many other features on this product to meet industry requirements. As the market tends to tailor thermal solutions with higher current density semiconductor materials, Dana engineers chose thermal resistance accordingly. Dana has therefore designed a unique cooling system specifically for these individual requirements. Power electronics engineers are also constantly seeking to achieve high durability against thermal fatigue. Overheating of the IGBT stamper may cause peeling of the inner layer to eventually fail. Dana's thermal solution limits the maximum temperature at the junction by maintaining the appropriate heat increase between the layers of the entire system. Not only that, this compact and innovative design can dissipate heat from both surfaces of the power module to achieve optimal performance. "We not only attach the heat sink to the IGBT products. We will customize a set of equipment according to the special configuration of performance requirements, and will be compact and lightweight." Dana Power Group Technology Business Development Manager Nick Carman said. In order to create such a precise heat dissipation product, Dana uses fluid-free continuous aluminum welding instead of messy solvent welding. Due to the addition of salts and ions in the process of solvent welding, it will react with the refrigerant, resulting in the accumulation of conductivity. Dana's patented fluid-free welding process ensures that the workpiece is clean by eliminating contamination and also maintains low conductivity of the heat dissipation fluid. By working with electronics manufacturers, Dana ensures that IGBTs can be matched to component interfaces in all models. Dana engineers improved bonding technology to install the interface layer to make better connectivity and optimize heat conduction. In addition, flatness is a key component interface. If not flat, it may cause the die to overheat. By reducing the contact resistance, Dana improves the thermal conductivity, thereby significantly improving the reliability of the vehicle.